6 min read
Induction Tooling – Advancements In Induction Heating Tooling Technology
Ajax TOCCO Magnethermic
:
August 3, 2007
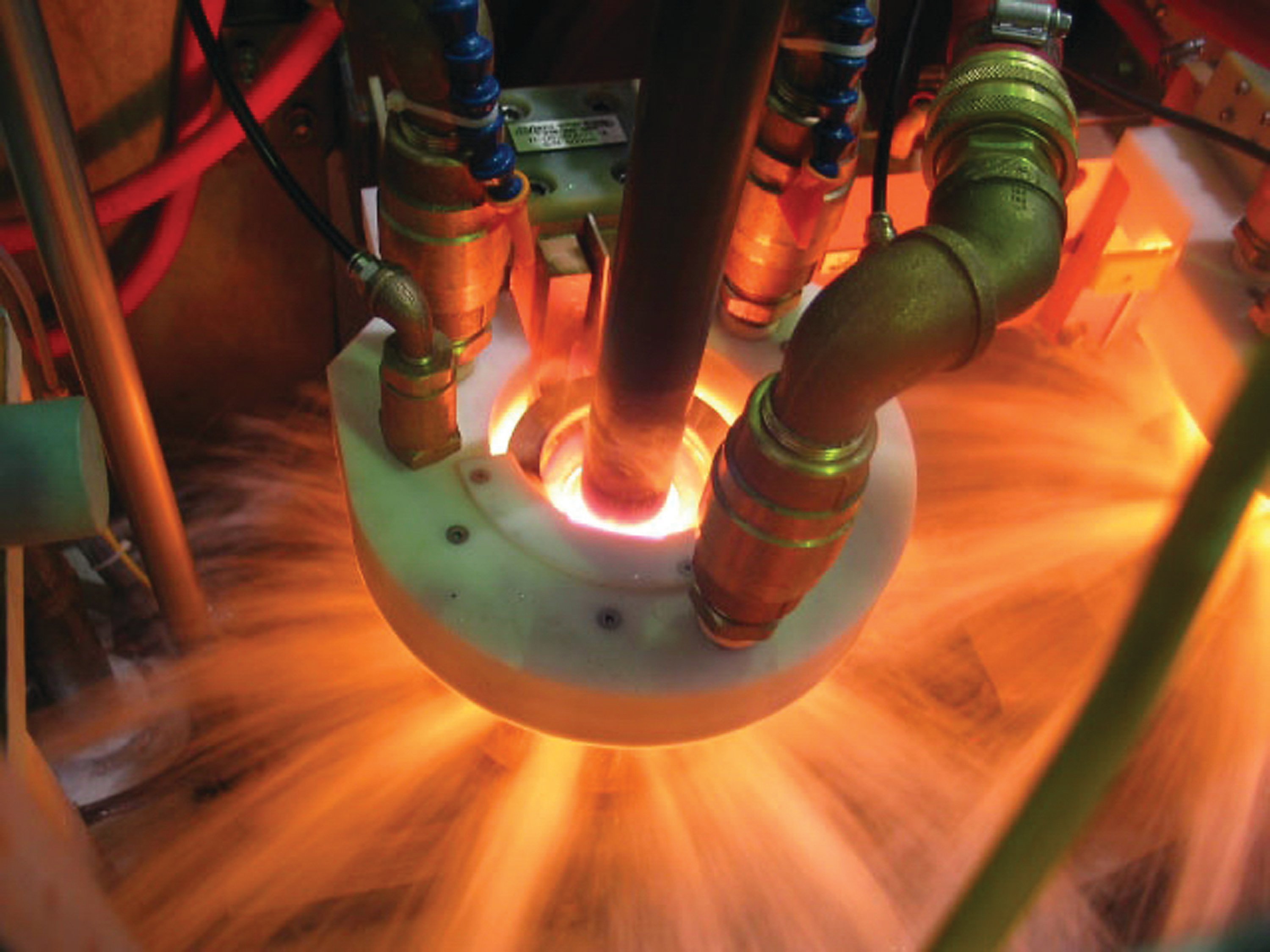
ASM International Publication, July/August 2006
George Pfaffmann, FASM, Ajax TOCCO Magnethermic Corp., Madison Heights, Mich.
The induction heating tooling industry has made progress in providing improved tooling capable of meeting user needs, but there still is a long way to go to advance the technology. Key to achieving these goals is the use of rational scientific techniques to reduce the laborious approach of empirical trial-and-error methods.
Induction tooling technology in its infancy primarily consisted of fabricated copper tubing construction which limited its advancement through the 1950s and 1960s. Subsequently, tooling generally was handled by small tooling fabricators and in-house facilities. In the meantime, many major induction heating manufacturers concentrated on developing new sophisticated high-frequency power generation equipment and integrated sophisticated automation equipment to achieve more efficient throughput. The sorely needed development of improved tooling having greater durability was hampered due to limited access to a true extended-term testbed facility to support evaluation and validation of tooling failure mechanisms. Also, design optimization and application analysis was unquestionably restricted due to the arduous use of trial-and-error methodology because of the unavailability of scientific computational tools.
Induction tooling technology has advanced since its early beginnings; its evolution is similar to that which has occurred in the machining equipment-manufacturing industry. Basic equipment, such as lathes, mills, machining centers, etc., is supplied by equipment manufacturers and tooling is supplied by separate vendors. However, induction tooling inductor coils and accessory components are highly application specific in the induction heating business, which requires proper analysis of factors such as the mechanical design to fit the handling/ automation equipment with required maintainability, reliability, and electrical/magnetic effect considerations to meet process specifications and needed durability. All of these mechanical engineering issues also require an in-depth understanding of induction heating electrical technology, induction heating application engineering, and metallurgical/thermal reactions. In today's highly competitive environment, these issues must also include a sound understanding of the interrelated economics involved in high-volume, high-speed automated handling facilities. This challenge is certainly just as important today in moving to integrate induction heat treating into highly flexible and even agile manufacturing work cells. The name of the game is to maximize uptime and ensure quality, which provides a high return on invested capital.
New Paradigms Required
This is a comprehensive and expanding set of challenges, in many cases exceeding the capabilities of past business models/operational structures and the existing empirical trial-and-error approach to creating solutions. Full-service induction heating equipment manufacturers need a complete range of tooling manufacturing operations with up-to-date in-house engineering resources; experience as a fully operational certified commercial heat treater is a valuable plus.
Induction heating equipment manufacturers also must recognize that the correct solution lies in using a structured scientific approach. Providing optimum solutions for the demands of today's industry requires using the latest advancements in computerized analytical procedures backed by a sound understanding of the mechanical, physical, electrical, and metallurgical science disciplines. Unfortunately, due to the number of interrelated variables to be considered involving all of the science disciplines, it is not a situation of one size fits all or readily available "plug-and-play" models. In addition, each situation is application specific as to requirements, specification window tolerance, production rates, and economics that are specifically tied to per-part tooling maintenance and durability costs.
Computerized Tools Need Further Development
There is an additional challenge in finding solutions to this requirement. Current computerized mathematical tools (FEA, FDA, and BEM) are still not fully developed to handle all the interrelated variables in a complete three-dimensional (3-D) format. Also, a complete set of materials characterization databases are not fully documented to support a full simulation analysis.
Carefully characterizing simulated processes and boundary conditions has long been recognized as important in modeling and simulation studies. As simulations improve, both users and modelers increasingly recognize the importance of having accurate, quantitative materials properties to drive their simulations. Simulation results cannot closely predict actual production results without accurate materials properties data, even when process data is accurate.
Recognizing the need for quantitative data for simulations, representatives of the steel, forging, and heat treating industries collaborated with the National Center for Manufacturing Sciences (NCMS, Ann Arbor, Mich; www.ncms.org) on a project to develop a method to quantitatively measure steel transformation data. The work resulted in the creation of ASTM International standard ASTM A1033-04: Standard Practice for Quantitative Measurement and Reporting of Hypoeutectoid Carbon and Low-Alloy Steel Phase Transformations (ASTM International, West Conshohocken, Pa.; www.astm.org).
The NCMS project was a start to fill this lack of data, but much work still needs to be done in collecting quantitative materials property data and storing them in an easily accessible, centralized database that can provide the data in proper formats for the different modeling programs.
Induction-heating engineers have had to develop specialized skills to manipulate existing formats to match the special conditions of each application. In addition, the application of existing computerized mathematical tools requires periodic first-hand actual validation tests to establish the validity of the applied format for the particular application model. Companies spending the time and effort in this area have developed these specialized skills coupled with validation resources and have the capability to address industry requirements. However, there currently are no readily available plug-and-play, fully capable models.
Modeling Challenges Ahead
Experience shows that accelerated thermal excursions possible with induction heating rates and intensive integral quenching rates produce unique refined microstructures that have improved properties. This is in agreement with the understanding by metallurgists today that the classic evaluation of mechanical properties by measuring hardness is no longer adequate. For example, Dr. Gerry Ludtka, Distinguished R&D Staff, Materials Science & Technology Div., Oak Ridge National Laboratory (ORNL) says "In modeling processes where predicting shape change/distortion, microstructure evolution, residual stress, and mechanical properties in the final component are the end goals, there are two intertwined critical data set needs: (1) phase transformation kinetic and dilation data, and (2) mechanical properties as a function of microstructure, temperature, and strain rate. Most folks (including the majority of modelers) do not realize that there is the potential for huge mechanical property (yield strength) discontinuities to occur when phase transformation occurs. Literally, for the parent austenite and product martensite phases, there can be a 15 to 50 times difference in yield strength depending on the alloy carbon level. When you couple that with the large dilation strains (2 to 4.6 vol% depending on carbon level and transformation products) that occur during the phase transformation, the interaction (things like transformation plasticity kick in) has major ramifications on the actual microstructure, distortion, and residual stresses that result in the quenched product."
Current State Of The Art
Advanced application computerized math tools. Computer simulation models optimize the induction coil geometry design to meet a specific thermal resultant profile. This must adequately characterize the dual-phase, magnetic/nonmagnetic phases of both the underlying core structure and surface volume portion together with transition zone plus the respective volume factions. These simulation studies produce optimum frequency, power densities, and heat times. Adjustments have to be made for phase transformation kinetics and required prior metallurgical structure austenit:izing temperature adjustments. Optimization of variables usually necessitates several iterations to meet the "what if" characterizations, which can be particularly time consuming proportional to the tolerance width of the blueprint specification. Because of the limited capability of these computerized tools and material databases, and the nonlinear interdependency of the multiple variables mentioned above, many of today's demands (other than the simple ones or those of a duplicate nature) required several integrated validated actual heat run tests with applied iterations of adjusted model simulations.
Equipment hardware advancements. Major advancements have been made in the flexibility of new solid-state, high-frequency power supplies including precise frequency selection and advancements in matching/tuning hardware. The use of modeling studies can capitalize on those innovative advancements to optimize the resultant hardness profile of part geometries and process productivity. Also, it provides improved inductor design parameters to reduce interrelated thermal and mechanical stresses on the inductor coil.
Inductor coil thermal transfer operational improvements. A critical factor in increasing inductor coil durability and life expectancy is directly related to the ability to adequately remove l2R heat losses generated by high current densities that flow through inductor coils. Therefore, the size, shape, and placement of the cooling water passages are critical. Inductor coils machined from solid copper with precisely machined cooling passages provide substantial additional flexibility to the coil designer. These fabrication methods can be economically applied to reduce thermal-related failures and provide a more effective design. Such coils are necessary for consistent quality performance to meet increasingly tighter user applications involving more complex parts and narrower tolerance windows on specifications.
Achieving the full benefit of these coil-design enhancements requires using the latest techniques in heat flux transfer calculations and cooling water surface velocities with controlled turbulence. Moving from conventional/convection cooling to properly controlled nucleative boiling can prevent laminar fluid flow stagnation and elevated thermal transfer. High current densities generated in the restricted confines of the inductor can result in thermally induced sequential microplastic deformation, which can result in tensile fatigue failures in copper (thermal ratcheting). Therefore, FEA modeling of the electrical current in the coil together with its dynamic shifts during processing must be analyzed to ensure safe operating limits.
Understanding Mechanically Applied Forces (Lorentz Forces)
Electromagnetic action set up by the inductor coil generates a reactive mechanical force between the part and the inductor coil that is inversely proportional to the selected frequency. These forces can be substantial, particularly in high-power applications. There is also a component of thermally generated mechanical forces within the induction coil. These forces must be considered in designing the supporting mechanism for the induction coil configuration to provide the necessary rigidity and mechanical position repeatability without having an adverse effect on coil operational durability.
The author has spent the majority of his 50+ career years working in the area of induction heating/heat treating technology, both as a practitioner and research scientist, and is deeply interested in raising the bar of understanding and continuing to move this technology ahead. He is a longstanding member of the ASM Heat Treating Society's R&D Committee, and actively promotes collaborative R&D to advance all heat heating processes from an experience-based technology to a more structured engineering/science-based technology. Your input and comments on the above discussion and/or on other aspects of induction heating technology needs and direction of research and development are solicited and welcomed.
Ajax TOCCO Magnethermic, a subsidiary of Park-Ohio Holdings Corp., designs and manufactures world-class induction heating and melting equipment for various industries and applications throughout the world. In addition, the company provides a range of services and offerings including laboratory process development, preventive maintenance, equipment repair and parts, coil repair facilities, and installation services through its locations in North America, South America, Europe, and Asia.
E-mail: info@ajaxtocco.com
Website: www.ajaxtocco.com